Ramping Up
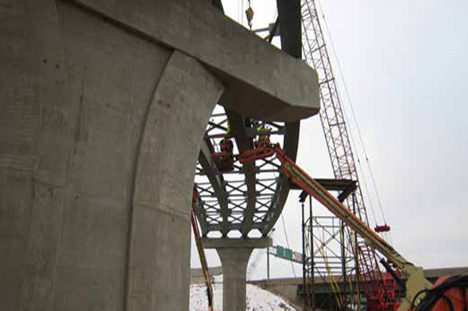
Every Metro Area includes intersections that drivers dread. For Twin Cities drivers, navigating the intersection of TH169 and I-494 meant traveling through three sets of traffic signals in short succession and dealing with frequent bottlenecks. (TH169 is a U.S. Highway; “TH” stands for “Trunk Highway.”) In addition to delays, the congestion in the interchange often resulted in traffic accidents. Improvements to […]